AI in Manufacturing
Transforming Industries with Predictive Maintenance, Automated Quality Control, and Supply Chain Optimization
The manufacturing industry is undergoing a transformation, and AI is at the heart of this revolution. No longer confined to research labs or futuristic dreams, AI is now a practical tool that manufacturers are leveraging to solve long-standing challenges. From minimizing machine downtime to ensuring product quality and optimizing supply chains, AI is driving efficiency and innovation across every stage of production.
This blog will delve into the three critical areas where AI is making a profound impact: predictive maintenance, automated quality control, and supply chain optimization. We’ll explore how these technologies work, provide real-world examples, and discuss their broader implications for the future of manufacturing.
1. Predictive Maintenance: Reducing Downtime and Costs
In traditional manufacturing, machinery breakdowns are a costly disruption. Repairs often occur after a failure, which can lead to significant downtime, missed production deadlines, and expensive repairs. AI-driven predictive maintenance is flipping this reactive model on its head by anticipating issues before they occur.
How Predictive Maintenance Works
Data Collection: IoT sensors installed on machinery gather real-time data such as temperature, vibration, and pressure.
- Data Analysis: Machine learning algorithms analyze this data to detect patterns that indicate wear and tear or impending failures.
- Alerts: When anomalies are detected, the system sends predictive alerts to maintenance teams, enabling proactive repairs.
- Key Benefits
Reduced Downtime: Machines spend less time idle, leading to uninterrupted production schedules.
- Cost Efficiency: Preventive repairs are significantly cheaper than fixing major breakdowns or replacing machinery.
- Extended Equipment Lifespan: By addressing small issues early, manufacturers can extend the life of expensive equipment.
- Enhanced Safety: Predictive maintenance helps identify potential safety risks, such as overheating or structural failures, reducing workplace accidents.
- Real-World Example
General Motors (GM): GM uses predictive maintenance systems in its factories to monitor critical equipment like welding robots. By analyzing sensor data, they’ve reduced unplanned downtime by up to 20%, saving millions annually.
- Why It Matters
Predictive maintenance not only ensures smoother operations but also contributes to a more sustainable manufacturing model by reducing waste and conserving resources.
2. Automated Quality Control: Ensuring Precision at Scale
Quality control has always been a critical aspect of manufacturing. Traditional inspection methods, however, are labor-intensive and prone to human error. AI-powered automated quality control is revolutionizing this process by using advanced technologies like computer vision and machine learning to detect defects with unparalleled accuracy and speed.
How Automated Quality Control Works
Computer Vision: High-speed cameras capture images or videos of products on the assembly line.
- Machine Learning Models: Algorithms analyze these images to detect defects, inconsistencies, or deviations from design specifications.
- Real-Time Feedback: The system flags defective items instantly, allowing operators to address issues immediately.
- Key Benefits
Increased Accuracy: AI systems can identify defects invisible to the human eye, such as microfractures or minor deviations in measurements.
- Faster Inspections: Automated systems can process thousands of items per hour, far outpacing human inspectors.
- Cost Reduction: By catching defects early, manufacturers can reduce waste and avoid costly recalls.
- Real-World Example
BMW: BMW’s factories use AI-driven quality control systems to inspect paint jobs and bodywork. The technology identifies scratches, dents, and other imperfections in real-time, ensuring only flawless vehicles leave the production line.
- Why It Matters
Automated quality control not only protects a manufacturer’s reputation but also improves customer satisfaction by ensuring consistently high-quality products.
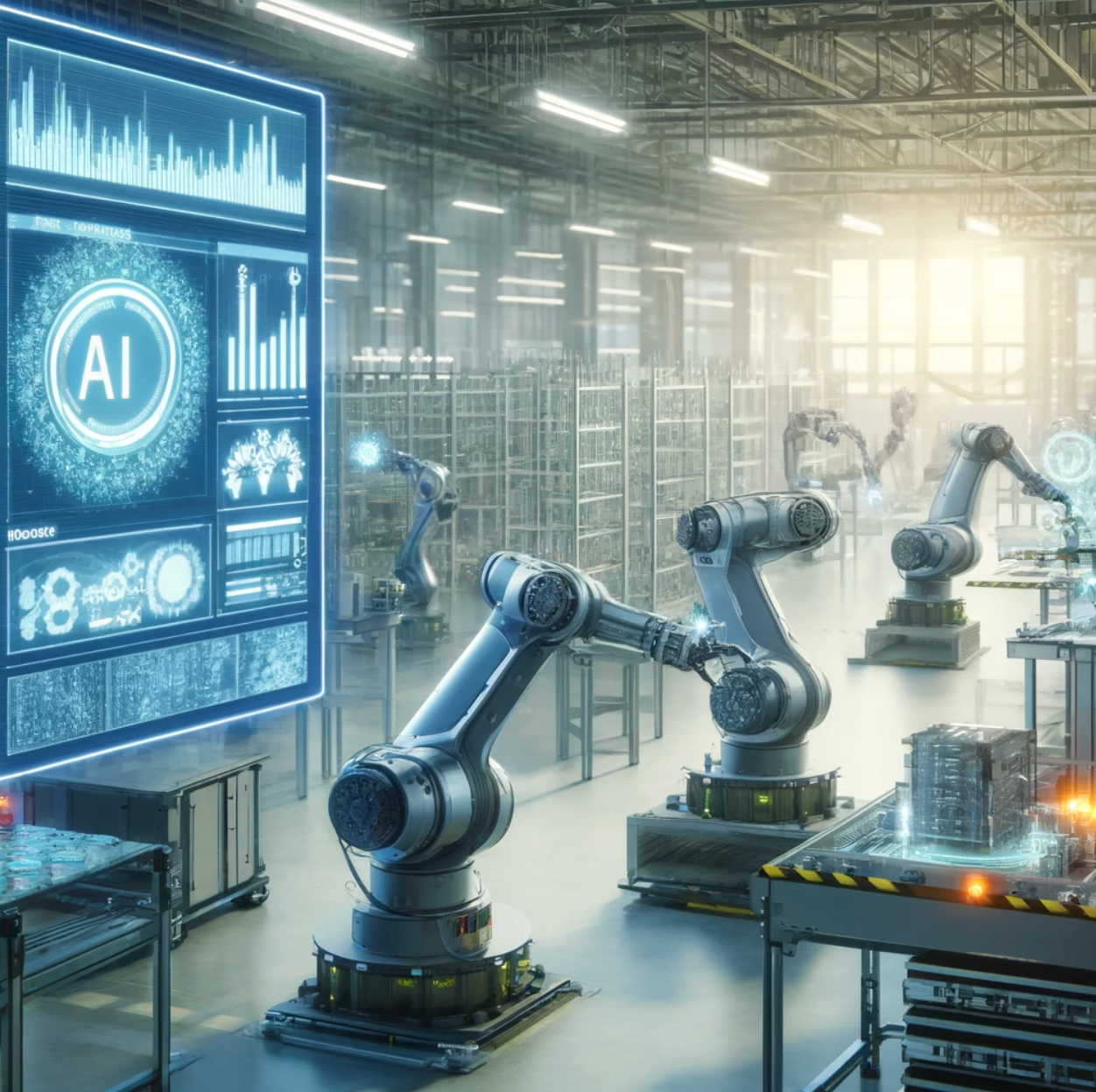
3. Supply Chain Optimization: Streamlining Operations
An efficient supply chain is the backbone of any successful manufacturing operation. However, traditional supply chain management often struggles with inefficiencies, bottlenecks, and unpredictable disruptions. AI is transforming this space by providing predictive insights, automating logistics, and improving inventory management.
How AI Optimizes Supply Chains
Demand Forecasting: AI analyzes historical sales data, market trends, and external factors like weather or geopolitical events to predict demand accurately.
- Logistics Optimization: AI-powered tools identify bottlenecks in transportation and suggest optimal shipping routes to reduce delays.
- Inventory Management: By tracking inventory levels in real-time, AI prevents overstocking and stockouts, ensuring the right products are available when needed.
- Key Benefits
Cost Savings: AI minimizes waste and reduces storage costs by optimizing inventory levels.
- Faster Deliveries: Efficient routing and scheduling improve delivery times and customer satisfaction.
- Resilience: AI enables manufacturers to respond quickly to disruptions, such as supply shortages or natural disasters.
- Real-World Example
Amazon: Amazon leverages AI extensively in its supply chain operations. From forecasting customer demand to optimizing warehouse storage and delivery routes, AI plays a pivotal role in ensuring seamless logistics for millions of daily orders.
- Why It Matters
AI-driven supply chain optimization enhances flexibility and reliability, enabling manufacturers to adapt to rapidly changing market conditions.
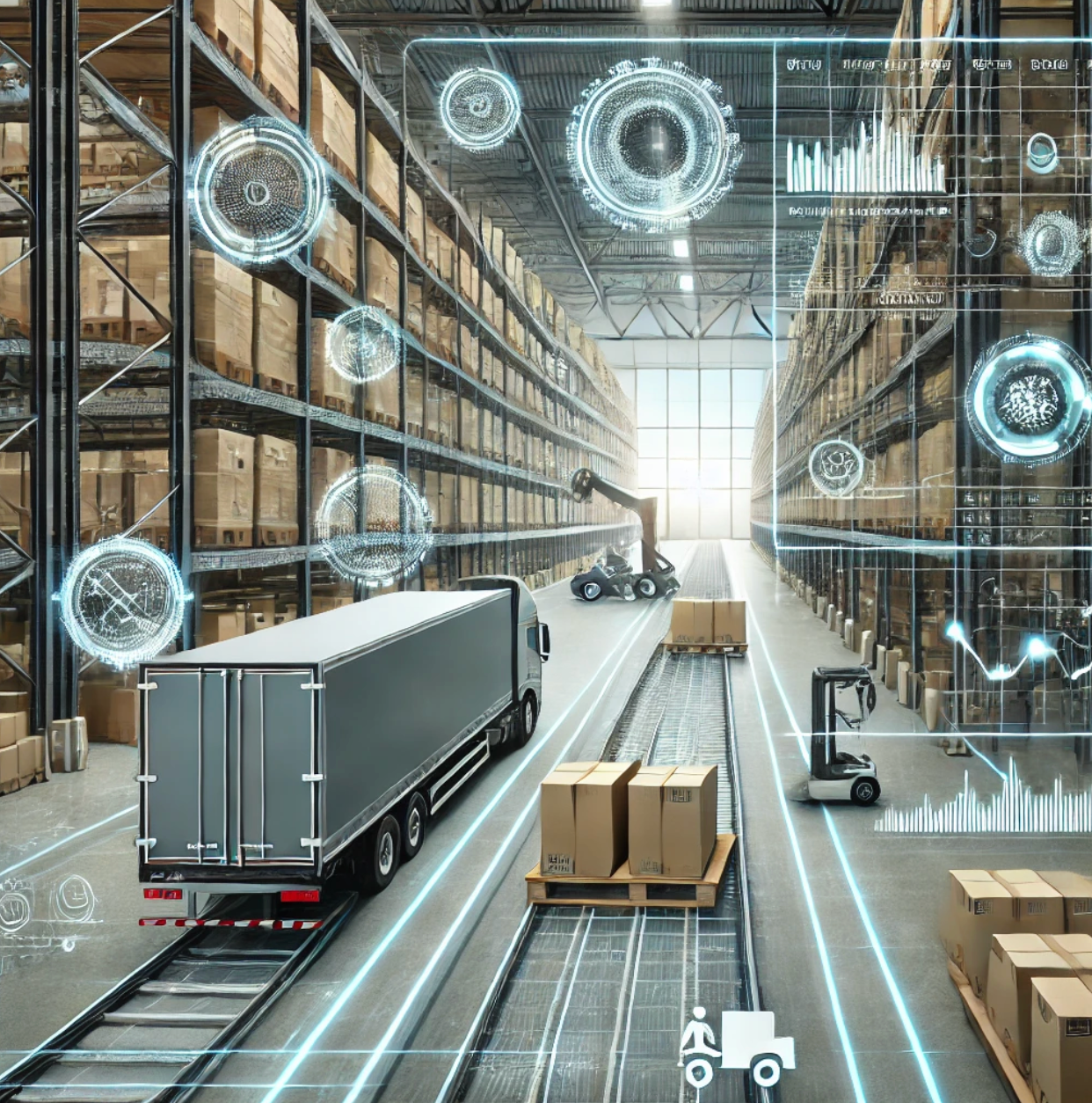
4. The Future of AI in Manufacturing
The integration of AI in manufacturing is just the beginning. As technology advances, we can expect even more innovative applications that will redefine the industry:
Mass Customization: AI will enable manufacturers to produce highly customized products at scale, catering to individual customer preferences without sacrificing efficiency.
- Sustainability: AI can optimize resource usage, minimize waste, and reduce energy consumption, helping manufacturers meet sustainability goals.
- Collaborative Robotics: AI-powered robots, or cobots, will work alongside humans to perform tasks that require both precision and adaptability.
- Challenges to Address
While the potential of AI is immense, manufacturers must navigate several challenges:
Data Security: Protecting sensitive production data from cyber threats.
- Integration Costs: Implementing AI systems requires significant investment in infrastructure and training.
- Workforce Transition: Upskilling employees to work with AI tools is essential to maximize their potential and mitigate fears of job displacement.
Final Thoughts: AI as a Game-Changer
The adoption of AI in manufacturing is not just a competitive advantage—it’s becoming a necessity. Predictive maintenance ensures machines run smoothly, automated quality control guarantees flawless products, and supply chain optimization enhances efficiency and resilience. Together, these advancements are setting the stage for a smarter, more efficient, and more sustainable manufacturing industry.
As manufacturers embrace AI, they not only reduce costs and improve productivity but also position themselves as leaders in a rapidly evolving market.
Stay Ahead of the Curve
Are you ready to explore how AI can revolutionize your industry? Sign up for our newsletter to receive exclusive insights, expert analysis, and the latest trends in AI and manufacturing. Join a community of forward-thinking professionals and stay informed about the innovations shaping the future. Subscribe now and take the first step toward a smarter, AI-driven tomorrow!
Sign Up For Our Weekly Newsletter and Get Your FREE Ebook " AI For Everyone - Learn the Basics and Embrace the Future"